【培养基的优化】灌流工艺的开发:用于灌流的培养基
在灌流操作中,除了对反应器环境,即进、出液流速,的可靠控制外,在极高的细胞密度条件下,还会出现多种工程挑战,如搅拌、通气、pH控制以及细胞聚集,其它的一些主要限制因素还包括所生产分子的特性,其又包括蛋白质的最大可允许滞留时间(其会限制反应器体积和灌流速率之间的比例)、最大的收获速率(受细胞截留设备的限制)、最高的细胞密度(受包括氧气供应等因素的限制)以及最低CSPR(受培养基配方及其维持细胞存活的能力的限制)。
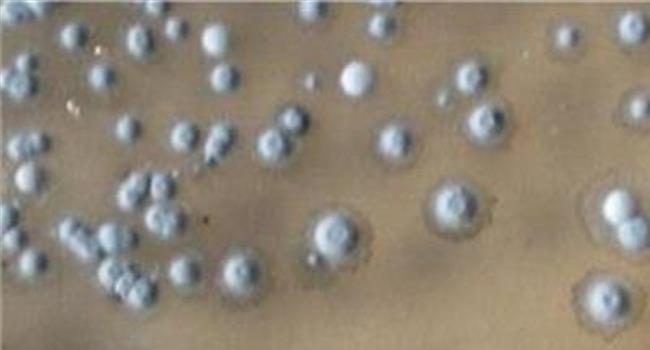
用于灌流的培养基
灌流流速是工艺性能的关键参数,其通常定义为灌流速率(每日罐体积,vvd-1)或细胞特异性灌流速率(CSPR,nL·cell-1·day-1)。一般情况下,为使培养基消耗最小化,目标是在与给定VCD值的稳态反应器操作相容的最低值下进行灌流操作,亦即CSPR最小化。
Konstantinov等介绍了一种“push-to-low”(推向更低)的策略,来评估用于某一灌流工艺的培养基的性能。他们的方法是先建立稳态状态,然后逐步降低CSPR,直到VCD或活性不可维持,从而确定最低值 - CSPRmin。
降低CSPR可通过降低培养基进液流速或提高生物质设定值来进行。为避免高细胞密度可导致的问题,如氧限制或细胞截留设备污染,建议在一个恒定且可维持的VCD条件下,降低培养基流速。
一旦知道理想的CSPR值后,灌流速率可根据细胞密度或生物质进行在线控制。已有科研人员将这种策略应用于N-1灌流生物反应器和浓缩补料分批工艺。虽然较高的灌流速率(如>2vvd)确实可以支持极高的细胞浓度,但这通常不是一种“方便”的方法,因为所需的培养基体积使其有点“不切实际”。
过高的灌流速率可能可用于快速提高生物质,如细胞库冻存或N-1灌流,但从经济性以及操作角度考虑,不建议用于生产阶段灌流生物反应器的长期维持。
为了降低高细胞密度工艺的培养基消耗,有必要对培养基成分进行优化调节。事实上,浓缩培养基可用于显著降低CSPRmin。从原理上讲,如果假定增加的营养物浓度以及降低的代谢物清除速率不会影响细胞代谢,特别是其产率,则如培养基浓缩2倍,维持相同的VCD时,灌流速率可降低2倍。
Yang等将该策略用于浓缩补料分批和N-1灌流。对于浓缩补料分批,两倍浓缩的培养基的结果并不理想。最高细胞密度高于其它补液策略,但是细胞没有从“生长”转变为“生产”。
而将两倍浓缩的培养基用于N-1灌流生物反应器则更加成功:由于增加的培养基浓度有利于细胞生长,尽管CSPR降低,生长速率仍提高。5天内达到目标细胞密度(40x10^6cells/mL),而使用其它策略需要6天或更长时间。
当然,培养基浓度与细胞生长速率之间的关系与细胞系的特性有关,代谢废物和细胞信号可在某一种环境设置下更快地驱动细胞生长。所以,了解不同细胞系的特性行为尤为重要,以便在进行培养基优化前,先确定哪种行为与灌流更加相关。
自生物生产出现以来,培养基开发就一直是细胞培养工艺开发和优化的最重要方面,给予其高度的优先级别不仅仅是出于工艺性能本身的考量,更重要的是出于安全性原因。第一款细胞培养基使用动物源性产品制备,这会将患者暴露于多种危险因素,例如病毒和朊病毒。
患者的感染性风险是非常重要的考量因素,特别是慢性疾病,因为患者需要连续用药。此外,由于批间差易所导致的工艺不一致性也是减少动物、甚至植物源性培养基成分的一个驱动力。这不是一项小工作,直到今天,仍有巨大的工作量被投入到化学限定培养基中新成分的鉴定,以增强细胞生长。
例如,酵母裂解物最近被分离和鉴定。生长因子,如多胺,被鉴定认为对细胞培养有积极作用。基于这些发现,酵母添加物可用已鉴定的化合物替代,并确保获得相似的细胞培养性能。化学限定培养现在已经有商业化的产品,而且,大多数的大型生物制药公司都会开发自己的配方。
该领域的发展还在继续。例如,高度浓缩的补液培养基非具有不小挑战,因为某些化合物的物理特性会有溶解性或稳定性的限制,工业补料分批平台中的半胱氨酸和酪氨酸就是一个很好的例子。半胱氨酸在中性pH条件下不稳定,而酪氨酸的溶解性极低。所以,鉴定了两者的衍生物,如硒代半胱氨酸和磷酸酪氨酸钠盐,以增加其各自在浓缩补液培养基中的浓度,从而维持相似的细胞生长性能。
由于灌流培养基变得越来越复杂和富集,浓度限值对其越发重要。McCoy等研究了用于灌流培养的浓缩培养基的稳定性,其将一种专利化学限定培养基浓缩了5倍,与由半胱氨酸、酪氨酸和叶酸组成的补液添加物一起使用。在评估了对不同化合物稳定性的影响后,得出的最佳选择是使用一种四部分系统,包括5倍的浓缩液、半胱氨酸/酪氨酸/叶酸添加物、谷氨酰胺和水。浓缩液可稳定一个月。
使用“解耦”灌流培养基的主意是另一种新的开发思路,即使用不同的进样液流,以更好地控制所需的特定营养物和灌流速率。Yang等将一种相似的方法用于浓缩补料分批的一种补液策略。灌流速率固定为1vvd,其组成包括基于每日葡萄糖检测控制的葡萄糖补液、由每日细胞计数控制的补液浓度以及一种基础培养基,以组合完成目标流速。
Lin等描述的一种方法是将补料分批培养基与补液混合,以获得一种更加浓缩的培养基。找到最佳比例并调节部分成分浓度和渗透压后,培养基“深度”增加了2倍。
这意味着,维持确定的细胞浓度,所需的灌流速率仅为之前的一半。结果是,在100pL/cell/day的CSPR下,获得了VCD约30x10^6cells/mL的细胞培养。
另一个灌流培养基优化的案例证明,提高灌流培养基中消泡剂(Pluronic)的浓度有益。增加消泡剂浓度,过滤设备中没有观察到产物截留。相反,由于培养液的活性保持不变,相比在低活性和低消泡剂浓度下的培养,产物截留被最小化。
上述案例说明,培养基开发仍是灌流细胞培养工艺开发的重点,事实上,为了开发连续操作模式的全部潜力,该领域还需要做更多的工作。目前市面上的培养基大多数是优化用于补料分批工艺,所以对于灌流操作来说,可能不是最佳选择。
例如,在补料分批操作中,刺激细胞生长的培养基成分是必不可少的,但在灌流工艺的生产阶段,可能不需要,甚至是有害的。灌流的独特性可能会需要特殊的培养基,在不同的工艺阶段(如N-1和N),甚至可能需要不同的培养基,以优化工艺性能和培养基成本。
不同培养基或补液液流的“解耦”可提供更多的灵活性,可能可实现对工艺更好的控制。例如,可以根据生物反应器内相关参数的在线监测,独立控制多个培养基成分。事实上,上述的每种概念,都有很大的潜力挖掘和优化空间。